Equipment Management and Safety for Managers in Care
Current Status
Price
Get Started
Buy Pay As You Go credits
- Pay as you go, buy credits and use on any course*.
- One credit gives you access to one course for one user from £1.99 a credit
- Unlock bigger discounts by purchasing more credits! – Use scroll bar below to review:
*Excluding Care Certificate and Management Courses
Cost per Credit: £8.50
Credits: 1. Total Price: £8.50
About the course
Proper equipment management is crucial in care settings, ensuring that service users receive safe, high-quality care while complying with legal and regulatory standards. Care managers play a critical role in overseeing equipment maintenance, risk assessments, emergency response planning, and compliance with CQC regulations under Regulation 15 of the Health and Social Care Act 2008 (Regulated Activities) Regulations 2014.
This course provides a comprehensive understanding of equipment safety, maintenance procedures, and legal responsibilities in care environments, including care homes and domiciliary care services. Learners will explore equipment risk management strategies, staff training requirements, and emergency protocols for equipment failures.
With increasing CQC inspections, safety regulations, and legal accountability, care managers must ensure that equipment is well-maintained, regularly inspected, and suitable for service users’ needs. This includes compliance with PUWER, LOLER, and electrical safety regulations to prevent avoidable harm.
By the end of this course, participants will be equipped to implement robust equipment safety policies, conduct risk assessments, oversee maintenance schedules, and respond to equipment failures effectively. This course is ideal for care managers, compliance officers, senior staff, and operational leads responsible for ensuring safe and effective equipment use in care settings.
What will you learn
Equipment Compliance and Regulatory Framework
Gain a thorough understanding of legal responsibilities and regulatory requirements in equipment management within care settings.
- Regulation 15 and Its Compliance Requirements
Learn the legal obligations for care providers regarding safe premises and equipment use, as enforced by CQC inspections and quality standards. - Key Equipment Safety Regulations (PUWER & LOLER)
Explore how PUWER and LOLER apply to care environments, including lifting equipment maintenance, inspection schedules, and staff training requirements. - Employer and Management Responsibilities in Equipment Safety
Understand the manager’s role in risk management, maintenance planning, and compliance documentation for audits and inspections. - The Role of CQC in Equipment Inspections
Learn how CQC evaluates compliance with Regulation 15, including maintenance records, risk assessments, and staff competency checks.
Equipment Risk Management and Maintenance Procedures
Develop essential risk management and equipment maintenance strategies to ensure safety and regulatory compliance.
- Creating Effective Equipment Maintenance Schedules
Learn best practices for preventative maintenance, including routine inspections, servicing timelines, and emergency repairs. - Occupational Therapists (OTs) and Equipment Suitability
Understand how OTs assess service users and provide adaptive equipment, ensuring continuous monitoring and adjustments to meet changing needs. - Incident Reporting and Risk Mitigation
Explore strategies for identifying equipment failures, documenting risks, and preventing safety breaches. - Equipment Storage and Organisation in Care Settings
Discover how proper storage solutions prevent damage, improve accessibility, and enhance response times in emergencies.
Managing Electrical Equipment and Emergency Protocols
Gain in-depth knowledge of electrical safety, emergency response, and power failure protocols in care settings.
- Common Electrical Equipment in Care Environments
Learn about oxygen concentrators, pressure-relieving mattresses, electric hoists, profiling beds, and other essential equipment. - Legal Framework for Electrical Equipment (Electricity at Work Regulations 1989 & PAT Testing)
Understand mandatory PAT testing, power failure planning, and fire safety precautions for life-supporting medical devices. - Emergency Response to Equipment Failures
Learn step-by-step procedures for responding to power outages, faulty medical devices, and electrical malfunctions in care settings. - Fire Prevention Strategies for Equipment Safety
Explore risk assessments, fire safety planning, and staff training in emergency response protocols for electrical and oxygen-related hazards.
Leadership and Continuous Improvement in Equipment Management
Develop leadership skills to drive compliance, quality improvement, and accountability in equipment safety.
- The Role of Leadership in Equipment Safety and Compliance
Learn how managers enforce policies, train staff, and embed a culture of accountability in equipment use and maintenance. - Continuous Improvement Strategies in Equipment Safety
Implement audits, incident reviews, and risk management plans to ensure high standards in care environments. - Developing a Reporting Culture for Equipment Safety
Encourage open communication, staff training, and digital reporting systems to prevent safety failures and legal non-compliance.
By completing this course, managers will be fully equipped to lead equipment safety initiatives, prevent hazards, and maintain compliance with regulatory standards in care settings.
Course Content
References
References
- Care Quality Commission (CQC). (2023). Key Lines of Enquiry (KLOEs). [Online] Available at: https://www.cqc.org.uk/guidance-providers/key-lines-enquiry-kloes [Accessed 11 Mar. 2025].
- Health and Social Care Act 2008 (Regulated Activities) Regulations 2014. (2014). SI 2014/2936. [Online] Available at: https://www.legislation.gov.uk/uksi/2014/2936/contents/made [Accessed 11 Mar. 2025].
- Provision and Use of Work Equipment Regulations 1998 (PUWER). (1998). SI 1998/2306. [Online] Available at: https://www.legislation.gov.uk/uksi/1998/2306/contents/made [Accessed 11 Mar. 2025].
- Lifting Operations and Lifting Equipment Regulations 1998 (LOLER). (1998). SI 1998/2307. [Online] Available at: https://www.legislation.gov.uk/uksi/1998/2307/contents/made [Accessed 11 Mar. 2025].
- Electricity at Work Regulations 1989. (1989). SI 1989/635. [Online] Available at: https://www.legislation.gov.uk/uksi/1989/635/contents/made [Accessed 11 Mar. 2025].
- Health and Safety Executive (HSE). (2023). Work Equipment and Machinery: PUWER and LOLER Guidance. [Online] Available at: https://www.hse.gov.uk/work-equipment-machinery/index.htm [Accessed 11 Mar. 2025].
- NHS England. (2023). Medical Equipment and Estates Management in Healthcare Settings. [Online] Available at: https://www.england.nhs.uk/estates/ [Accessed 11 Mar. 2025].
- Care Quality Commission (CQC). (2023). Health and Safety Compliance in Adult Social Care. [Online] Available at: https://www.cqc.org.uk/guidance-providers/adult-social-care [Accessed 11 Mar. 2025].
- Local Government Association (LGA). (2023). Best Practices for Equipment Safety in Care Settings. [Online] Available at: https://www.local.gov.uk/ [Accessed 11 Mar. 2025].
- British Standards Institution (BSI). (2022). BS 7671: Electrical Wiring Regulations for Care Environments. [Online] Available at: https://www.bsigroup.com/ [Accessed 11 Mar. 2025].
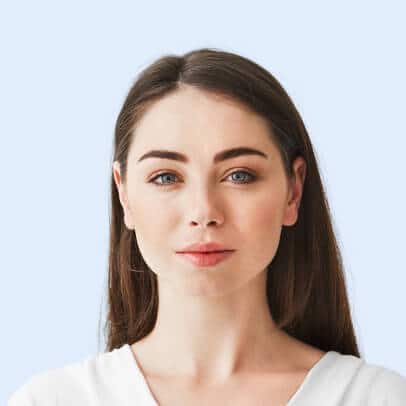
“Duis aute irure dolor in reprehenderit in voluptate velit esse cillum dolore eu fugiat nulla pariatur. Excepteur sint”
Katherine Cutts
Junior Designer at Company
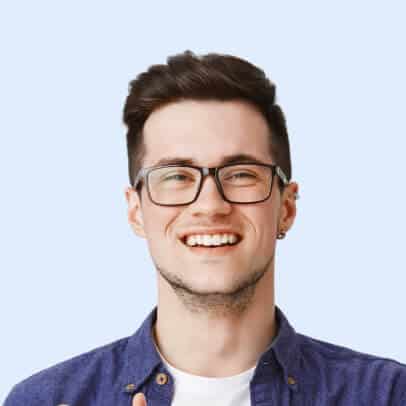
“Duis aute irure dolor in reprehenderit in voluptate velit esse cillum dolore eu fugiat nulla pariatur. Excepteur sint”
Daniel Smith
Mobile Developer at Busines
Ratings and Reviews
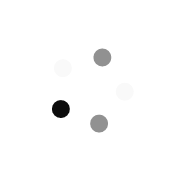